A Quick Guide to Cobalt Connectors (with lots of pictures!)
- Damon McMillan, Founder
- Feb 22, 2021
- 7 min read
Updated: Oct 29, 2021
Blue Trail Engineering's Cobalt connectors entered the market in late 2019, and have continued to receive overwhelmingly positive feedback from customers all over the world. In this quick guide, I'll share some pictures of Cobalt connector installations so that you can see the many different ways that they are used, and then answer some frequently asked questions.
But before getting into all that, let's first answer the question, "What makes Cobalt connectors different from other waterproof connectors?" Here are the main differences:
No potting or overmolding: Most other subsea connectors use potting or overmolding to make the waterproof seal between the connector shell and the electrical contacts. In Cobalt connectors, however, the pins/sockets are press-fit into a PEEK plastic connector core which is then press-fit into the connector shell. No potting or overmolding is required. Similarly, our Cobalt cables utilize a robust mechanical seal between the cable jacket and the connector shell. The cable jacket consists of high-quality polyurethane tubing with a smooth inner wall, which fits over a barbed shank on the connector shell. This makes Cobalt connectors more simple and more reliable than potted/molded connectors. In some cases, customers want to put a Cobalt connector on their own cable. For these situations we offer a cable termination kit that does require a simple potting operation, but even then the potting can be done by an amateur without the need for a mold or any special equipment.
Immediate availability: We ship the vast majority of our orders within 2-3 days. Custom items or large orders may take a week or two, but we are striving to cut the lead time as much as possible.
Low cost: Because of their unique design, the manufacturing of Cobalt connectors is relatively quick and does not require special equipment or tightly-controlled potting/overmolding processes, thus reducing cost.
Small size: Cobalt connectors are significantly smaller than other subsea connectors, both in diameter and length. This makes it easy to integrate them into smaller marine robotics projects. The Cobalt bulkhead connectors also have M10 threaded shanks instead of 7/16-20 threaded shanks, making them compatible with Blue Robotics products.
Cobalt connectors and cables are available in 3-pin, 4-pin, 6-pin and 8-pin versions.
The one limitation of Cobalt connectors is that they are not wet-mateable. If you absolutely need to connect and disconnect your connectors underwater, you'll have to use a SubConn-style connector.
What are the different ways that you can use Cobalt connectors?
Let's start by looking at the Cobalt bulkhead connector. It is waterproof in the open-face (unmated) condition, although we always recommend inserting a cable or dummy plug into the bulkhead connector before going underwater. The images below, courtesy of Marcus Gregson at Spot X in Australia, shows our Cobalt bulkhead connectors installed on his gorgeous underwater camera system.

And here are some bulkhead connectors used on an ASV autopilot enclosure:
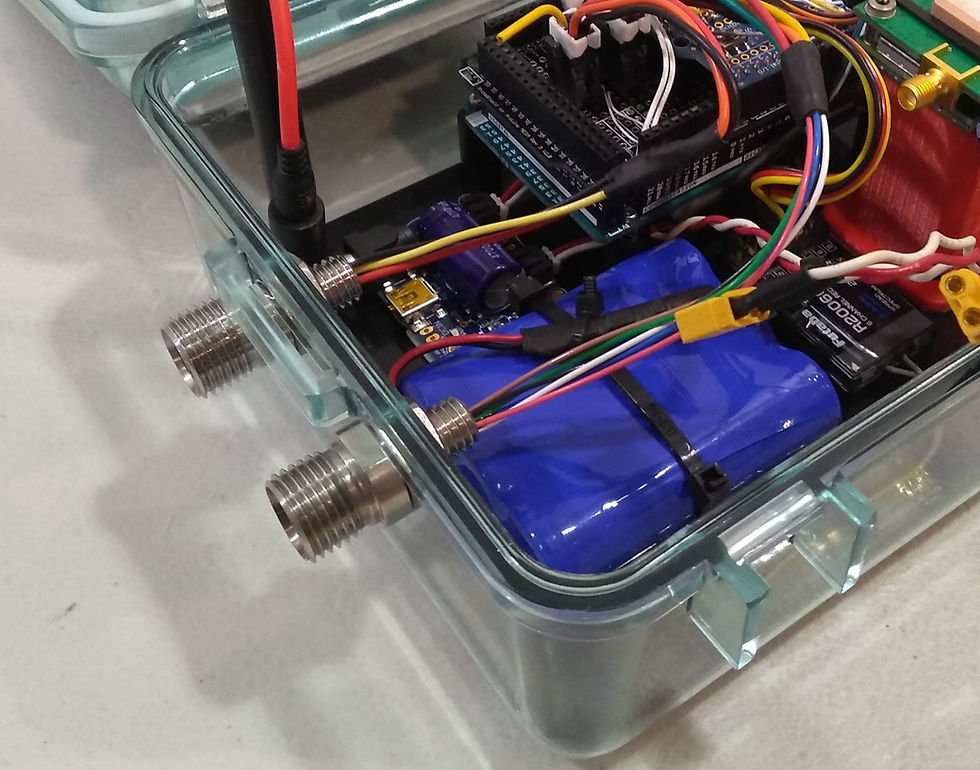
With a bulkhead connector in place, it is easy to connect a Cobalt cable to your device by mating the connectors together and tightening the acetal plastic locking sleeve (included with all of our cables). The connectors have flat surfaces that ensure proper orientation as you mate them together.
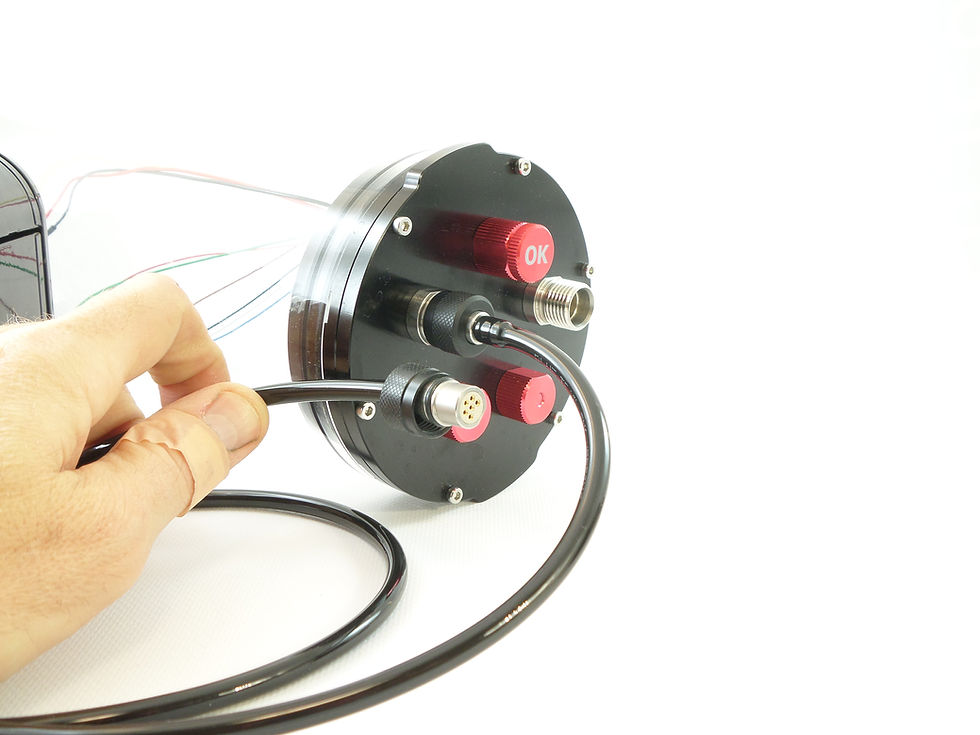
While it's nice to be able to connect and disconnect a cable in just a few seconds, you often don't need a quick connect/disconnect capability on both ends of the cable. In this case, you can make a semi-permanent connection on one end of the cable using a Simple Penetrator. The Simple Penetrator is, well, simple: it's just a barbed bulkhead fitting pressed into the cable jacket that screws into a hole in your device. Because Cobalt cables use smooth-walled polyurethane tubing as their cable jackets, the interior of the cable jacket creates an extremely reliable seal to the barbs on the Simple Penetrator. The result is a waterproof connection that is far less expensive than using a connector. There is a downside to Simple Penetrators, however: unlike a bulkhead connector, they do not form a waterproof barrier themselves: if the cable jacket gets cut, water will travel down the tubing, through the Simple Penetrator, and into your device.
We offer cables with a Cobalt connector on one end and a Simple Penetrator on the other end. We also offer Simple Penetrators by themselves (with either M6 or M10 threads) for those of you who want to make your own cables and connections.

Simple Penetrators make it easy to connect multiple devices inexpensively and reliably. For example, the picture below shows a set of Blue Robotics Lumen lights connected together with M6 Simple Penetrators and 6.4-mm tubing. In this case, the cable running through the tubing is a shielded 4-conductor cable, with two wires for power (shared by all of the lights) and the other two for brightness control (one wire for lights 1 and 2, and the other wire for lights 3 and 4). The chain of lights is connected to the ROV using a Cobalt connector (lower left).
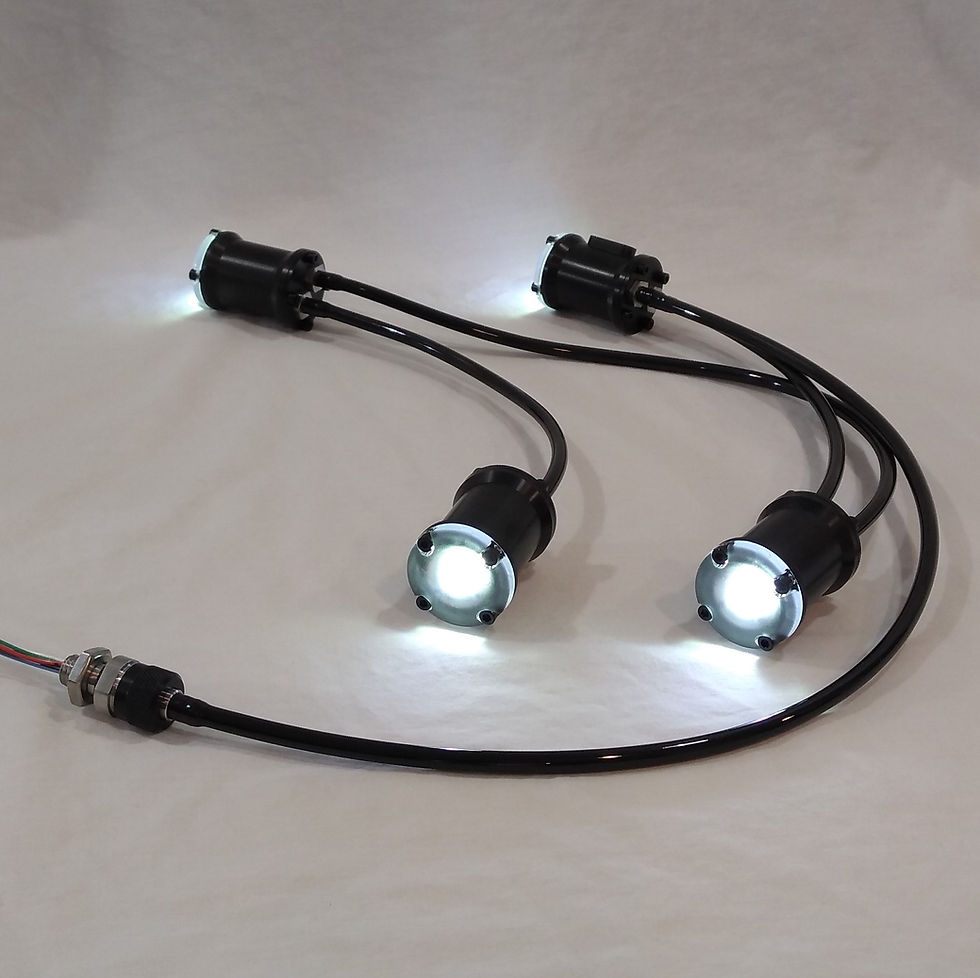
What if you want to install a Cobalt connector on your own cable? In this case, you can use a Cable Termination Kit. The cable termination kit consists of a stainless steel connector shell, acetal locking sleeve, O-ring, and PEEK insert with the electrical contacts pre-installed.

Unlike our stock Cobalt connectors and cables, the cable termination kits do require potting. After soldering the wires to the electrical contacts, you assemble the connector and inject epoxy or urethane into the connector shell (see directions here). You can put a cable termination kit on almost any cable that has a bondable cable jacket (such as polyurethane or neoprene).

Below is a picture from one of our customers, Shaun Graham at Cawthron Institute in New Zealand. He used cable termination kits in a fluorometer project (the blue rings you see at the end of the cable shells are custom 3D-printed parts that Shaun used to make the potting look nice and tidy).
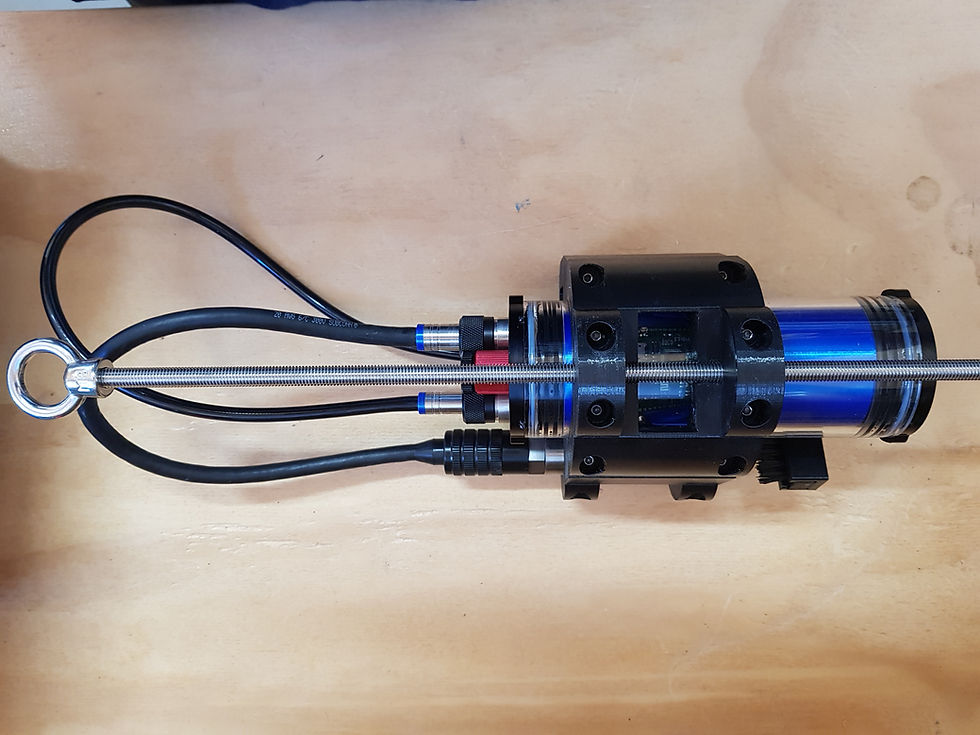
Cobalt connectors and cables integrate seamlessly with many Blue Robotics products. For example, the pictures below show:
Newton gripper with Cobalt cable and Simple Penetrator (this picture shows an older, anodized aluminum version of the Simple Penetrator -- all Simple Penetrators are now made from 316 stainless steel)
Replacement battery cable for BlueROV2 made from 4-pin Cobalt connectors and cable
Fathom tether with 8-pin cable termination kit
Still haven't found what you're looking for? In that case, give us a call and let us know your requirements. We can often make custom cables, such as the 1-pin connectors and cables shown below, which are used for high-current applications (>100 amps).
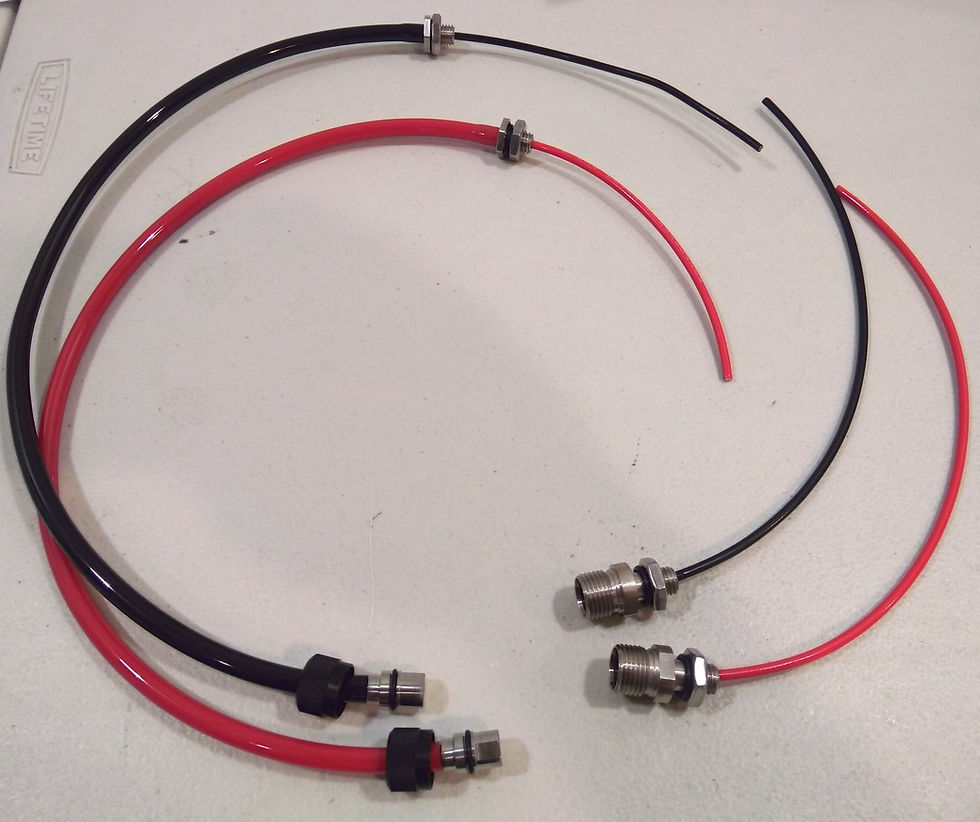
Finally, before getting to our FAQ section, I'd like to show some of the accessories that we have for Cobalt connectors:
Removable Locking Sleeve: The standard locking sleeve that comes with our cables and termination kits is held captive on the cable (you can't remove it or re-install it). But sometimes you need to be able to remove the locking sleeve, for instance if you need to fish the cable through a small hole. In this case, just use a Removable Locking Sleeve. This is similar to the locking sleeves found on other subsea connectors: it uses an internal retaining ring (actually just a plastic split washer) that is installed after you slip the locking sleeve over the connector. Note that the Removable Locking Sleeve only works on the "regular" size of cable termination kit, not on the "large" size.
Dummy Plug: Insert the Dummy Plug into a bulkhead connector in place of a cable. This protects the bulkhead connector from contamination and ensures that it will be waterproof to 600 meters.
Dummy Cap: Install the Dummy Cap on the end of an unmated cable. Same thing here: it both protects and ensures waterproofness.
Frequently Asked Questions (FAQs)
How do you determine the current rating for your connectors? We base the current rating of our connectors on the manufacturer's rating for the electrical contacts (pins and sockets) used in the connectors.
Can Cobalt connectors be used for 400-volt systems? We have not tested Cobalt cables and connectors to 400 volts, and we do not recommend using them at any voltage above the rated voltage of 100 VRMS / 150 VDC. This voltage rating is based on the creepage distance between pins/sockets in our connectors. Exercise extreme caution when using any voltage above 30 volts, especially near water, as these connectors have metal shells and semi-exposed contacts.
Do the connectors have an open-face depth rating? No. All of our connectors are designed to be waterproof up to 600 meters in the open-face (unmated) condition, but due to manufacturing tolerances we do not guarantee an open-face depth rating. However, in the closed-face (mated) condition, all of our connectors are rated to 600 meters.
What is the depth rating of the cables? Our Cobalt cables, just like the connectors, are rated to 600 meters. However, you might see the cable jacket squish a little if you take them to this depth since there is some air space inside the cables. This should not affect the performance of the cable.
What is the depth rating of the Simple Penetrators? The Simple Penetrators themselves are rated to 600 meters. But the tubing/cable jacket that is attached to the Simple Penetrator may squish at depth. Best practice is to make sure that the wires fill the inside volume of the tubing/cable jacket as much as possible to keep the tubing/cable jacket from squishing.
Why do you have female sockets on the cable connectors and male pins on the bulkhead connectors? The female sockets tend to be longer and larger in diameter than the male pins, and thus do not fit inside the bulkhead connector due to the limited space inside the M10 threaded portion of the connector.
What is the potting I see inside the threaded portion of the bulkhead connectors? This is epoxy. It is put there to provide strain relief to the wires and to prevent small bits of metal from getting inside and causing a short. It is NOT required to make the connectors waterproof.
Why do you only offer cables in a limited range of lengths? Our cables are made of high-quality polyurethane tubing with wires inserted into the tubing. This method allows us to install the connectors onto the cables without potting or overmolding. However, it does mean that there is a limit to how long we can make the cables (you can only push wires into the tubing so far). For double-ended cables, there is also a lower limit on the cable length due to the manufacturing process. If you really need a longer or shorter cable, give us a call. We know some tricks.
Any other tips? Make sure to lubricate the connectors, including O-rings, before using them. They may go together easily without lubricant, but will almost certainly be difficult to separate later.
Comentarios